- Online only
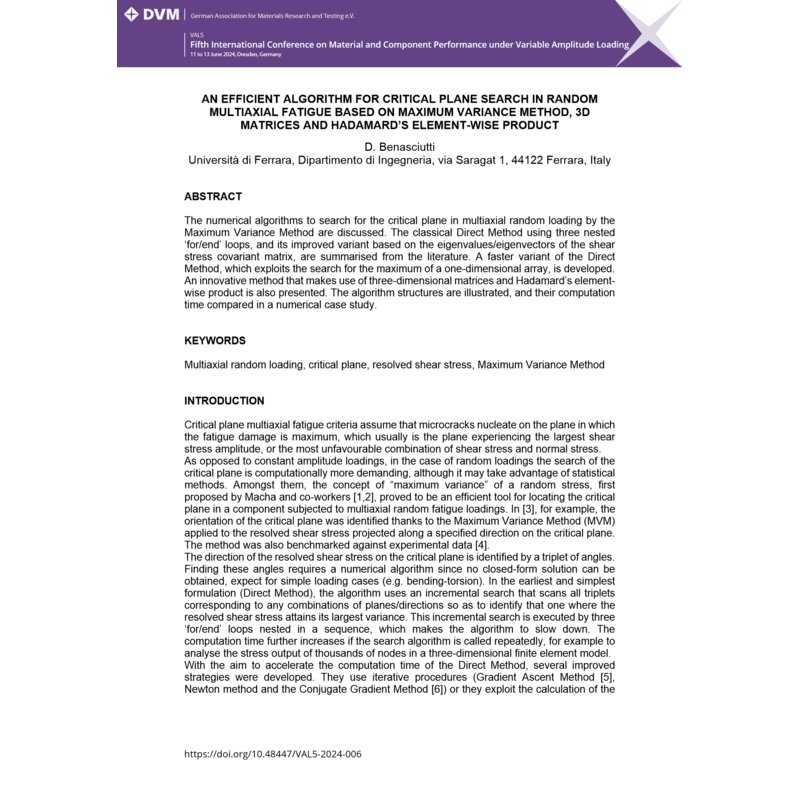
In multiaxial fatigue, critical plane criteria assume that microcracks nucleate on the plane onto which the fatigue damage is maximum, which usually corresponds to the plane experiencing the largest shear stress amplitude, or a combination of shear stress and normal stress. While with constant amplitude loadings the critical plane search is somehow straightforward, it becomes definitively more challenging with variable amplitude and random loadings, where statistical aspects come into play and make the critical plane search computationally more demanding.
In Ref. [1], the critical plane location has been located thanks to the Maximum Variance Method (MVM) applied to the resolved shear stress, i.e. the shear stress projected along a direction on the critical plane. The resolved…
Datenschutzbedingungen (bearbeiten im Modul "Kundenvorteile")
Lieferbedingungen (bearbeiten im Modul "Kundenvorteile")
Rücksendebedingungen (bearbeiten im Modul "Kundenvorteile")
In multiaxial fatigue, critical plane criteria assume that microcracks nucleate on the plane onto which the fatigue damage is maximum, which usually corresponds to the plane experiencing the largest shear stress amplitude, or a combination of shear stress and normal stress. While with constant amplitude loadings the critical plane search is somehow straightforward, it becomes definitively more challenging with variable amplitude and random loadings, where statistical aspects come into play and make the critical plane search computationally more demanding.
In Ref. [1], the critical plane location has been located thanks to the Maximum Variance Method (MVM) applied to the resolved shear stress, i.e. the shear stress projected along a direction on the critical plane. The resolved shear stress direction on the critical plane is identified by three Euler angles, see Figure 1 (left). The accuracy of the method has been tested against experimental data [2].
The point discussed in this paper is, however, the computational efficiency of the critical plane search when the resolved shear stress criterion is used in combination with the MVM. In its original formulation, the approach requires that a huge number of planes, corresponding to any possible combination of Euler angles, are analysed in order to identify those experiencing the maximum variance of the resolved shear stress. In a numerical algorithm, this task is usually accomplished by a sequence of nested “for/end” loops, which make the algorithm very time consuming, see Figure 1 (right). Over the years, some Authors have proposed various strategies (e.g. Gradient Ascent Method [3], Newton method and the Conjugate Gradient Method [4], eigenvalues/eigenvectors [5]) with the aim to shorten the computational time. Such strategies, however, still rely on iterative searching algorithms (as use of “for/end” loops) that represent the bottleneck of the overall searching procedure.
In the present paper, instead, a very different and efficient approach is adopted which makes the critical plane identification very fast, regardless of the requested resolution of Euler angles. This task is accomplished by means of three-dimensional matrices and Hadamard’s element-wise product, without any use of “for/end” loops. The computational efficiency of the proposed approach is benchmarked with the other existing algorithms mentioned above.