- Nur online erhältlich
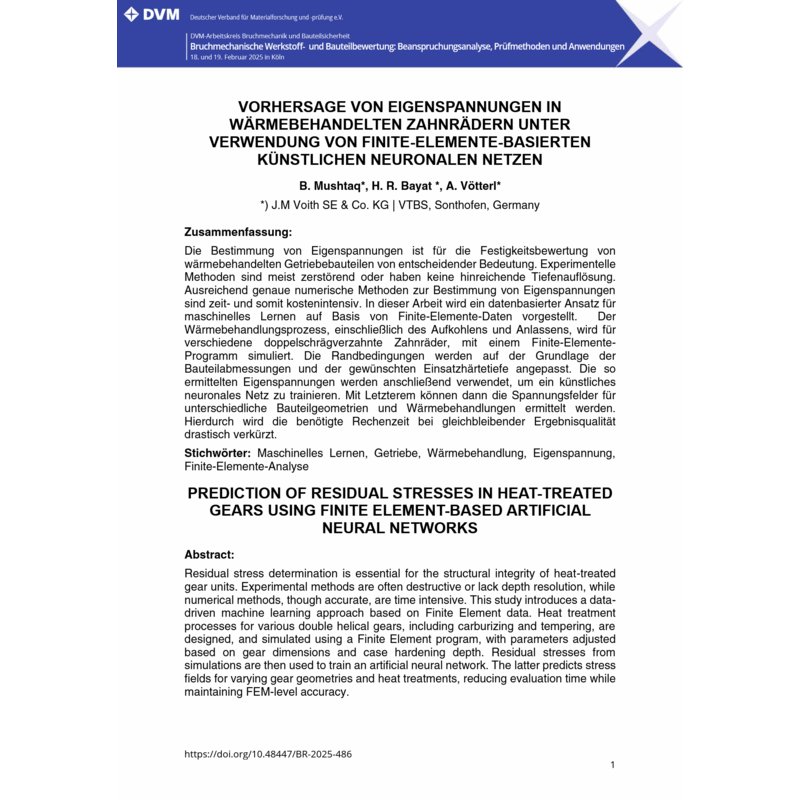
Determination of the residual stresses resulting from heat treatment processes, such as case hardening, is crucial for the structural integrity assessment of gear units. Experimental methods like deep hole drilling (DHD) are costly, time-consuming, and destructive, while non-destructive methods such as ultrasonic testing offer limited depth resolution. Advances in finite element methods (FEM) provide a promising alternative that does not damage the component. However, each FE computation can take over ten hours, depending on the complexity of the heat treatment and component geometry. By applying a data-driven machine learning approach, one can reduce the computation time from hours to a few seconds.
In this work, heat treatment for various double helical gears is designed…
Datenschutzbedingungen (bearbeiten im Modul "Kundenvorteile")
Lieferbedingungen (bearbeiten im Modul "Kundenvorteile")
Rücksendebedingungen (bearbeiten im Modul "Kundenvorteile")
Determination of the residual stresses resulting from heat treatment processes, such as case hardening, is crucial for the structural integrity assessment of gear units. Experimental methods like deep hole drilling (DHD) are costly, time-consuming, and destructive, while non-destructive methods such as ultrasonic testing offer limited depth resolution. Advances in finite element methods (FEM) provide a promising alternative that does not damage the component. However, each FE computation can take over ten hours, depending on the complexity of the heat treatment and component geometry. By applying a data-driven machine learning approach, one can reduce the computation time from hours to a few seconds.
In this work, heat treatment for various double helical gears is designed and simulated using a commercial FE program. These results are then validated against available data from deep-hole drilling (DHD) experiments. The heat treatment design involves carburizing, hardening, and two tempering cycles, with carburizing and tempering times adjusted based on gear dimensions and case hardening depth (CHD). The FE-based residual stresses are used to train and validate an artificial neural network (ANN) regression model to predict stresses at arbitrary locations for different gear dimensions with their respective heat treatments. Applying the ANN model in fracture assessment significantly decreases evaluation time while maintaining accuracy comparable to FE simulations as well as ensuring safe and reliable operations even at higher pitch line velocities.